Cadpro boosts design-and-build process for 13th Element
For 13th Element Fabrication, custom post-processing using Fusion by Autodesk creates flawless flow from design and drawings to CNC machinery.
Project Location:
New South Wales, Australia
Software Used:
Autodesk Fusion®, Nesting and Fabrication Extension
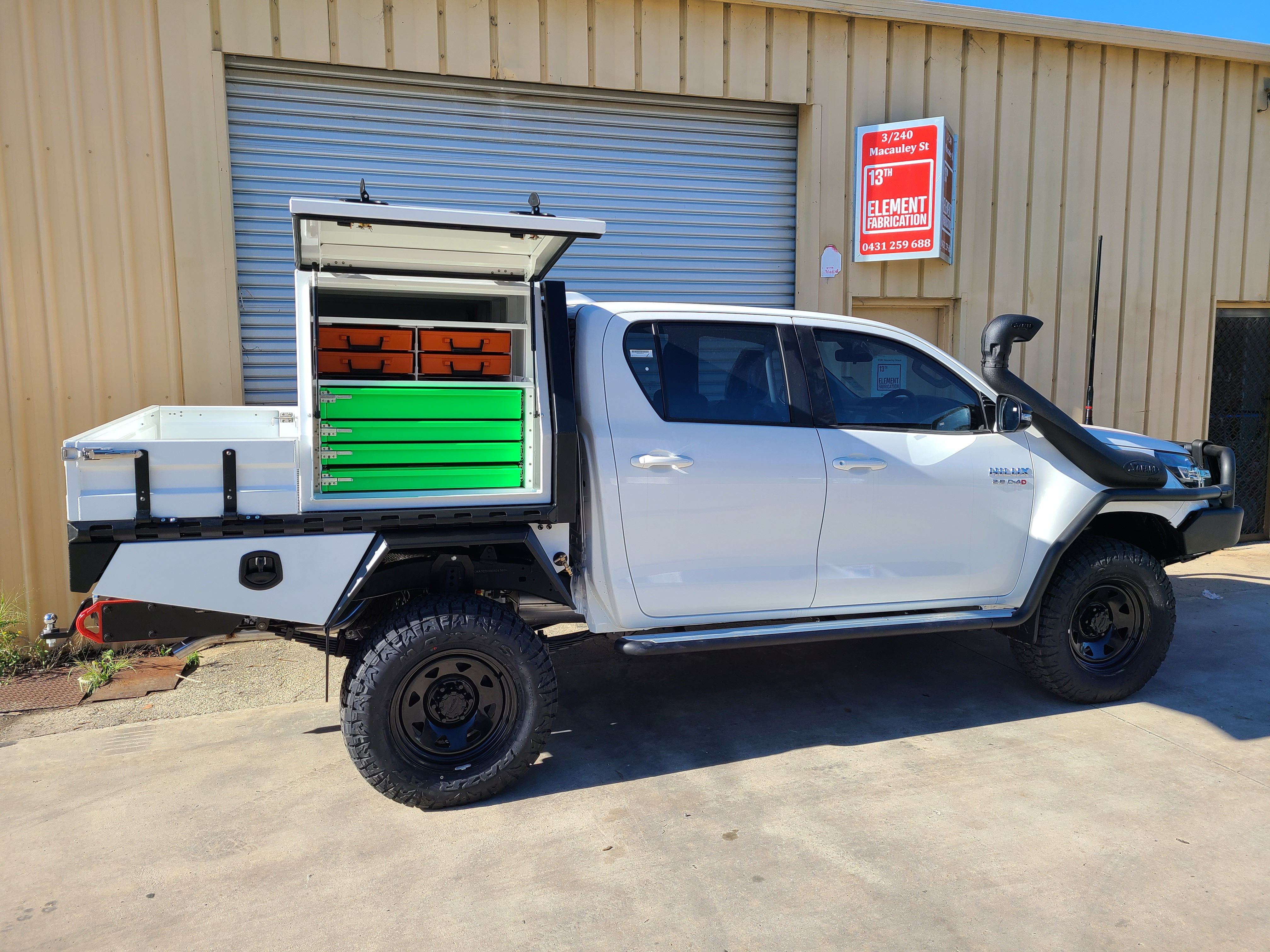
Customer challenge
Located in South Albury, New South Wales, 13th Element Fabrication designs and builds ute trays and canopies. Founder and managing director Nic Reilly customises each and every ute fit-out for his clients, from canopies, dog-boxes, drawers, shelves, latches and tie-downs to roof-racks and cooling vents. The company name refers to aluminium – the thirteenth element in the periodic table and Nic’s metal of choice, being light, robust and endlessly recyclable.
This ‘low volume, high variety’ business model is made possible through the use of CNC machinery powered by Fusion, Autodesk’s cloud-based 3D modelling platform, which supports the production pipeline from design right through to fabrication.
Nic was facing issues, however. As he puts it, ‘In layman’s terms, I couldn’t get Fusion to talk to my CNC correctly.’ He refers to the post-processor, the interface between computer and CNC machine, which wasn’t performing as required for his specific CNC router. ‘And that’s where Cadpro came in – to provide the specialist consulting and training we needed to get our software and equipment talking.’
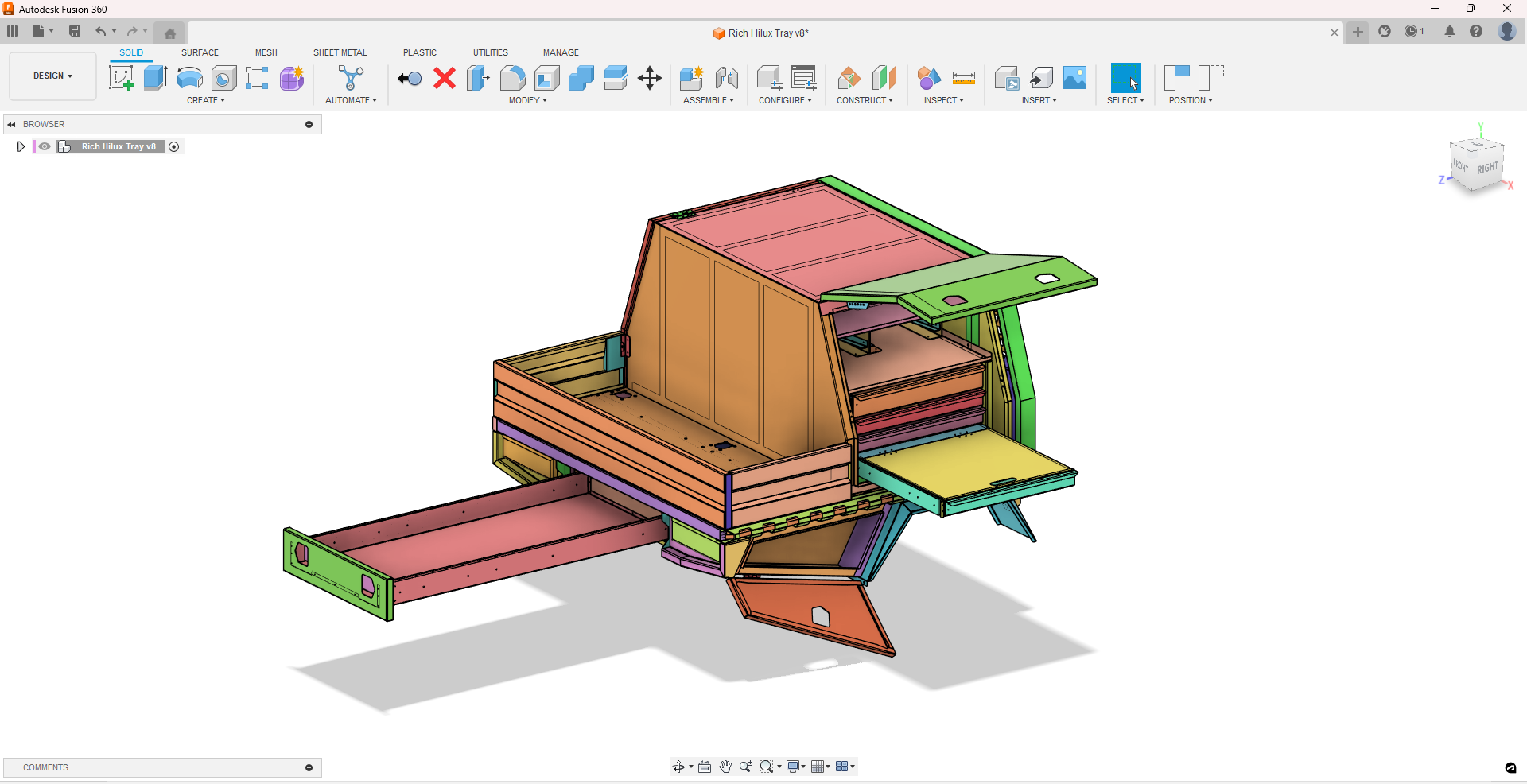
Project goals
To use the full range of products to good effect, Nic engaged Cadpro to design and build a post-processor tailored precisely to his set-up. This would enable seamless workflow from initial design right through to sending the G-code – the programming language used by CNC and 3D-printing equipment.
Nic bought his Fusion licence through Cadpro, along with the Nesting and Fabrication Extension. In acquiring the full range of products, his goal was to stay within the same program from start to finish, streamlining his workflow.
“Working with them (Cadpro) on the post-processor design was a very smooth and easy process. I was amazed at how much they knew about the machines I use.”
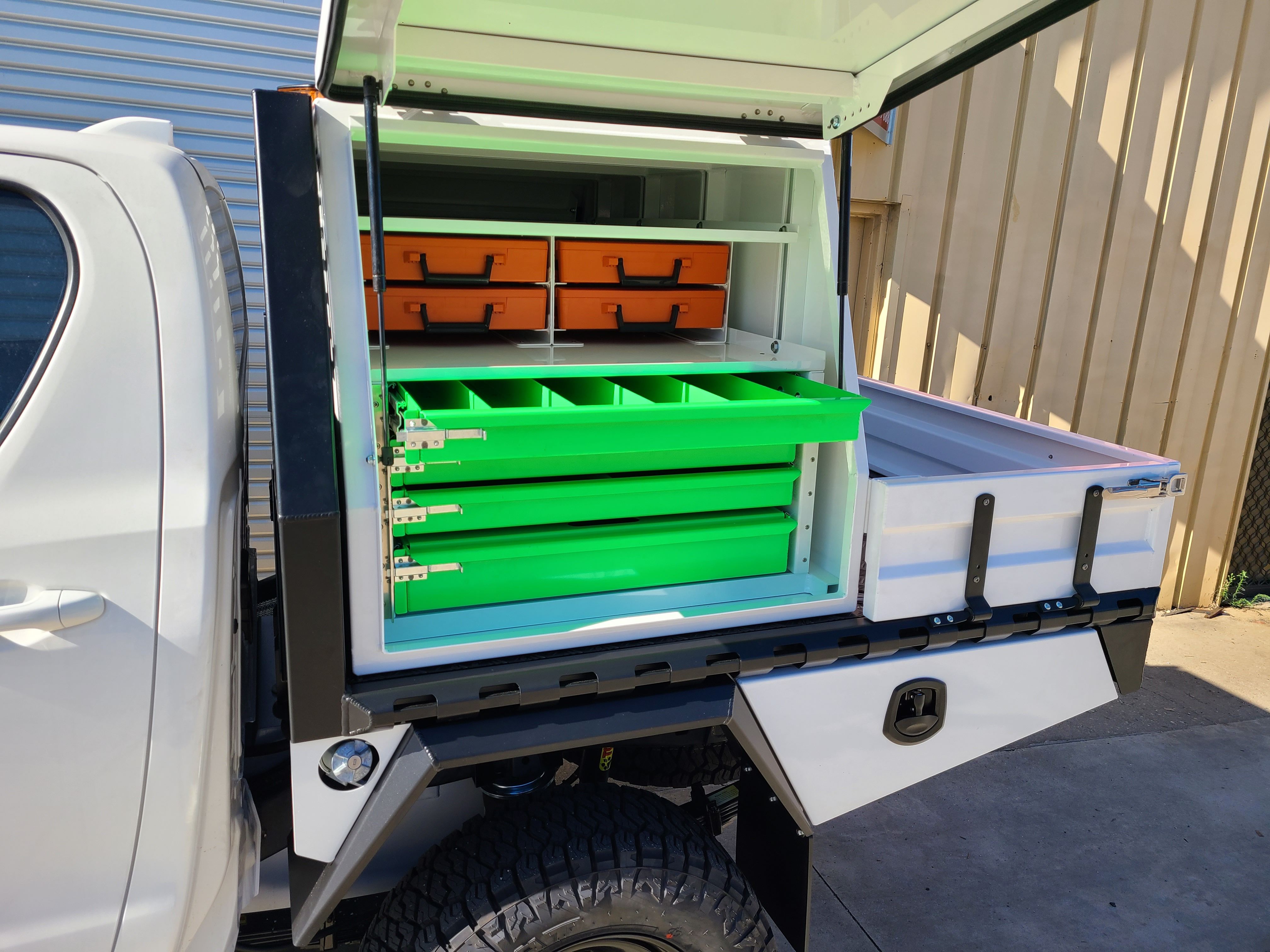
Solution
First, Cadpro asked Nic to send samples of what his machinery needed – the specific G-code. Next, they gave him samples to try out. With Cadpro’s intimate knowledge of CNC equipment, says Nic, working with them on the post-processor design was ‘a very smooth and easy process. I was amazed at how much they knew about the machines I use.’
The solution from Cadpro will benefit not only Nic, but also other users – and this, he says, ‘makes it very cost-effective. They build it once for me, and then on-sell it to others, so I don’t get landed with the full development costs. It’s genius.’
While Nic hasn’t needed to reach for the phone often, he has been impressed by their service offering. ‘Once, their New Zealand-based consultants came over and dropped in on me, and we went through things in person, one-on-one. I’ve been able to follow up with questions via email, too, and there’s always the phone. Their communication is good.’
Business outcomes
With the new post-processor installed, says Nic, ‘it’s one easy flow from design to a semi-finished product – and sometimes even the finished product’.
‘Because I do everything in-house, I love being able to prototype and test designs rapidly. I can very quickly design something on Fusion and go from CAD to CAM to CNC router via the post-processor. Having it all in the one program makes it smooth and fast.
‘I know the post-processor is capable of more, too, and it’s a huge help that I can phone Cadpro to either change the post-processor or help me with any of my Fusion needs.’
Nic comments that, with the post-processor correctly programmed, his CNC router works perfectly now – and as a Fusion user with a list of satisfied clients, he’s back in his element.
Learn more about 13th Element